|
|
Well, it's
started. Although I'm excited about seeing that new Mustang II crossmember under the
frame.. I've been dreading the removal of the Volare Clip. Perhaps a little history
is in order here. When I first got my beauty I had been reading everything I could
find on modifications for her. One of the favorite suspension choices was the
"Volare" clip. Actually it is nearly any Chrysler product that had a bolt
in front clip. Everyone I talked to and all I read said that this was a easy,
inexpensive way to upgrade from straight axle manual steering to independent front power
steering. And, it was true... for about $200.00 I was in business. We fabbed
engine and transmission mounts for a 2" offset. We thought there would be ample
room with that offset for everything. Everything looked good until I ordered a set
of Sanderson ceramic coated headers for my 460. After installing them I only had
3/16" of clearance at the steering box, and that was after trying three different 460
headers on the left side ! I knew that when the engine torqued the headers would
bang on the steering box and I really didn't want my $400 + headers banging on anything
! |
The truck was already at this
point... |
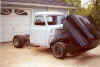
|
Cab was installed, steering
complete, front tilt operational, all brake and fuel lines run and connected. Engine
and transmission had been set and all mounts were complete. All of this had to be
removed and set aside or removed to be replaced. One nice Sunday afternoon I did
just that. Removed the front flip and set it on the other side of the garage.
Using an engine hoist I removed the cab (after disconnecting steering, brakes and master
cylinder)and set it on a rolling cart to move it to the other side of the garage
also. The engine/transmission was last and it was set on another set of rollers and
also pushed to the other side of the garage with everything else... it's getting crowded
over there now. |
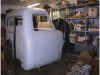 |
My wife asked me at lunch that day,
how long I'd been working on this truck and I really didn't remember. After looking
it up I found that it was the seventh anniversary of it's arrival on my place. Seven
years... and it took me about 5 hours to back up six of those years to what you see
here..... |
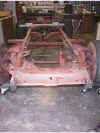 |
This was taken before the brake and fuel lines had been removed and
the shots below show those lines |
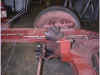 |
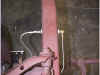 |
Our next step is to set it up on jackstands (it's on
wheel dollies now) and remove the front suspension components, tires, wheels and upper
control arms so we can access as much of the weld as possible. Then with the plasma
cutter cut as closely as we can to the subframe. There are places where a torch will
have to be used due to lack of space for the plasma gun. We welded the subframe in
solid on both frame rails and to the front cross member, so we've got a lot of cutting to
do. The boxing plates will have to be removed and replaced after the MII cross
member is installed... the old ones will be useless, so that will be another cut around
the top of the frame rails. |
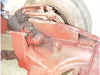 |
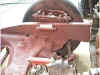 |
So, now the frame
is up on jack stands and stripped of most of the suspension, and all the lines.
We're ready to start cutting.. I've transferred the axle centerline to the frame, so
we have a reference for the new install. Heidt's uses the front spring shackle hole
as it's reference point.. and measures back 19-3/4" to the cross member
centerline. Since that portion of the frame was removed to install the volare clip..
we lost the reference. But, the rear spring mount holes are still there and
according to the Ford shop manual it is 41" between these points center to
center. Some simple math 41-19-3/4=21-1/4" from the center line of the rear
spring hanger, should put us at exactly the same place. A quick check from the rear
axle center line should give us 111" total wheelbase. The kit moves the wheels
forward one inch adding to the original 110" wheelbase. |
Day 2
(not consecutive) |
We've walked around
it a couple of times and we're ready to start the surgical removal of the Volare
clip.. I want to be careful about the cutting, someone might be able to use this
clip and I want all the cuts to be in the frame or boxing plates. We fire up the
compressor, plasma cutter, oxy/actl torch, drag out hammers and prybars and start flailing
and burning. About an hour later the clip (with the aid of a floor jack) slides to
the floor. The frame rails are hacked up pretty well. We had done a very, very
good job putting it in. Funny how the smallest little tack weld can hold so well
and be so hard to find. The pictures below show the drivers side frame rail after
the removal. Ok, so it's not so surgical, but it ain't there anymore. I've got
to admit I'm a little puckered up about the condition of the frame rails, but Dave assures
me that we can fix it 'as good as new'. If you've never read any of my other
articles you don't know Dave. He is a master fabricator and builder of much sought
after drag cars. His job description at work is a maintenance utilityman. It
means he an expert in electrical, hydraulic, mechanical and piping repairs. If you
can show him or tell him what you want to do... he can do it or build it. He never ceases
to impress me. I am very fortunate to have him helping me with my project...
and, I probably owe him the rest of my active life. I'm afraid to ask ! When you look at
the picture below, pay no attention to the opposite frame rail.. the picture was taken
after we had started putting in the patches. But, if you do look you can see how
well the patches are going in the frame. The pictures below show a side view of the cut
made to remove the volare clip and a front shot showing the 'gutted' frame
rails. The lower pictures show the cuts necessary in the front cross member to
remove the Volare clip.. All of these cuts will be patched and invisible when
completed. |
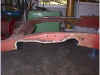 |
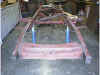 |
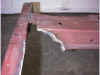 |
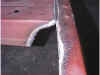 |
We mark the frame
rails with soap stone to square up the cuts and clamp a piece of angle iron along the cut
line. We'll use that angle as a straight edge for the plasma cutter to
follow. A few minutes later we have a nice square hole in the frame rail that
had once been what you see above. I didn't get a picture of the squared hole... but
the second picture shows what you should come up with... |
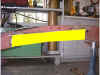 |
Our original plan
was to use 2x4 rectangular tubing... cut out two sides and we'd have a nice "L"
shaped patch piece with a nice radiused edge. Well, we all know about plans. |
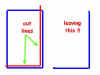
|
The frame rail at this
point, drops down 2-1/2" on the upper and lower edge and shrinks down from
about 5-3/4" down to 3-1/4". all these curves and shrinks killed that
idea. Seperate patch panels were patterned and cut. You just gotta love plasma
cutters. The pictures below show the cardboard patterns and the patches in the
rails. Another will be used to mend the lower portion of the rail. You can see
them in the other pictures. |
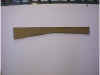 |
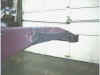 |
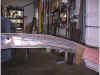 |
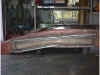 |
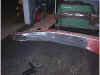 |
|